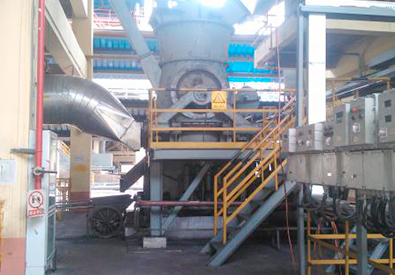
VRM integrates grinding, drying, sorting and conveying, which greatly simplifies the process flow. Compared with the traditional ball mill, the vertical mill can significantly reduce energy consumption and metal wear, and bring considerable economic...
As a kind of high efficiency grinding equipment, vertical roller mill is widely used for grinding various materials with high requirements of fineness and energy efficiency.
The grindability is from easy grinding to difficult grinding, and the grinding
energy consumption is from 4kwh / T to 25kwh / T.
The moisture content of the material ranges from 1% to 25%.
From non abrasive materials to highly abrasive materials.
From non cohesive materials to highly cohesive materials.
Through continuous optimization of structure design, andI company has successfully applied vertical roller mill technology to the grinding system of the following materials, and has accumulated rich practical experience in mill design and grinding system engineering
Preparation and injection system of pulverized coal for blast furnace, rotary kiln
and hot blast stove
Anthracite and coke blending process
Grinding of cement raw materials and clinker
Grinding of granulated blast furnace slag
The material is fed into the center of the rotating grinding plate through the rotary feeder (or sealed weighing feeder) and the feeding trough, and the metal foreign matters are separated from the material before reaching the rotary feeder. Under the action of centrifugal force, the material diffuses to the annular grinding roller table of the grinding plate. After being rolled by the grinding roller loaded by the hydraulic elastic system, it further moves to the edge of the grinding plate. The hot air is evenly distributed around the grinding plate through the air ring, and the milled and to be ground materials are blown up by the air flow at the air ring and dried. During the rising process of the mill, due to the gravity separation, the coarse particles fall back to the grinding plate, and the fine particles are carried to the separator by the air flow.
With the help of the separator blade, the material is divided into coarse powder and fine powder. The coarse powder falls back to the grinding plate for regrinding, and the fine powder flows out of the mill along with the gas and is collected in the powder collecting device of the system, which is the qualified product.
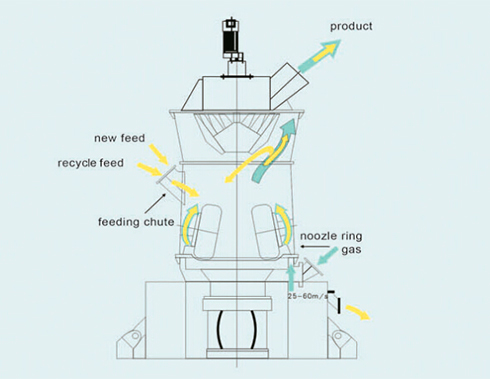
-
Grinding mechanism
The driving device is composed of motor, coupling and reducer. When starting the mill, the grinding roller can be lifted by the hydraulic cylinder. No matter with or without material, the mill can be started with light load without auxiliary starting device.
he reducer adopts a reliable bevel gear planetary gear structure. The axial thrust bearing supporting the grinding plate and grinding pressure is designed with multiple pieces. The thrust pads are immersed in the oil pool, and the lubricating oil is cooled and filtered through the lubrication station.
-
Hydraulic elastic loading system
The driving device is composed of motor, coupling and reducer. When starting the mill, the grinding roller can be lifted by the hydraulic cylinder. No matter with or without material, the mill can be started with light load without auxiliary starting device.
he reducer adopts a reliable bevel gear planetary gear structure. The axial thrust bearing supporting the grinding plate and grinding pressure is designed with multiple pieces. The thrust pads are immersed in the oil pool, and the lubricating oil is cooled and filtered through the lubrication station.
-
Grinding roller and table
The driving device is composed of motor, coupling and reducer. When starting the mill, the grinding roller can be lifted by the hydraulic cylinder. No matter with or without material, the mill can be started with light load without auxiliary starting device.
he reducer adopts a reliable bevel gear planetary gear structure. The axial thrust bearing supporting the grinding plate and grinding pressure is designed with multiple pieces. The thrust pads are immersed in the oil pool, and the lubricating oil is cooled and filtered through the lubrication station.
-
Nozzle ring
The driving device is composed of motor, coupling and reducer. When starting the mill, the grinding roller can be lifted by the hydraulic cylinder. No matter with or without material, the mill can be started with light load without auxiliary starting device.
he reducer adopts a reliable bevel gear planetary gear structure. The axial thrust bearing supporting the grinding plate and grinding pressure is designed with multiple pieces. The thrust pads are immersed in the oil pool, and the lubricating oil is cooled and filtered through the lubrication station.
-
Drive system
The driving device is composed of motor, coupling and reducer. When starting the mill, the grinding roller can be lifted by the hydraulic cylinder. No matter with or without material, the mill can be started with light load without auxiliary starting device.
he reducer adopts a reliable bevel gear planetary gear structure. The axial thrust bearing supporting the grinding plate and grinding pressure is designed with multiple pieces. The thrust pads are immersed in the oil pool, and the lubricating oil is cooled and filtered through the lubrication station.
-
Separator
The driving device is composed of motor, coupling and reducer. When starting the mill, the grinding roller can be lifted by the hydraulic cylinder. No matter with or without material, the mill can be started with light load without auxiliary starting device.
he reducer adopts a reliable bevel gear planetary gear structure. The axial thrust bearing supporting the grinding plate and grinding pressure is designed with multiple pieces. The thrust pads are immersed in the oil pool, and the lubricating oil is cooled and filtered through the lubrication station.
The rated output of the mill is determined by the grindability of the material, the required product fineness, water content and system operating conditions (such as the temperature of dry gas, air volume, etc.).
The grindability is usually specified according to the Hardgrove Grindability Index (HGI). The energy consumption of an ANDE mill depends on the grindability of the material and the product fineness, which is shown in the grindability diagram. Throughput of same mill size for different materials may vary greatly.
Mill model: ARM + material English code + mill plate medium diameter- roller quantity
Material English Code: Coal - no "material English Code"
Granulated blast furnace slag – s
Cement clinker – C
For example: ARM19-2, coal mill, medium diameter of grinding plate, 1900mm, two sets of grinding roller
Arms26-3, slag mill, medium diameter of grinding plate 2600 mm, 3 sets of grinding roller
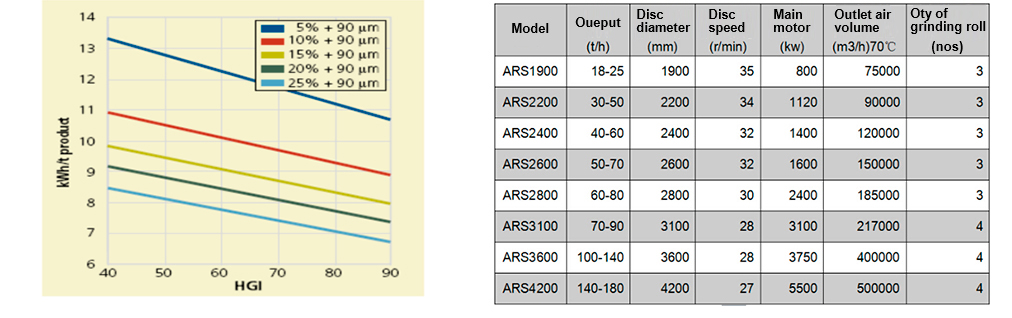