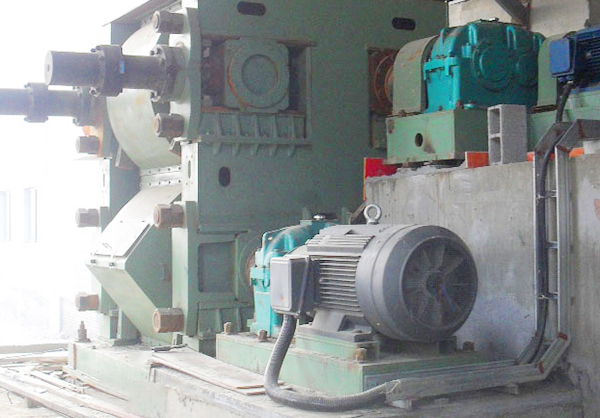
Double roll & Four roll crusher are used for crushing low/medium hardness materials with advantages of compact size, uniformity of final product size and low ratio of over-crushing.
Double roll crusher is primary crusher for material, reduced from (-)80 mm to (-)25mm, with crushing ratio up to 5:1.
Four roll crusher is an integrator of primary and secondary crushing. The size of material can be reduced directly from 40mm to (-)3mm with crushing ratio up to 10:1.
Double-roll crusher
The material from inlet drop into the middle of two work rolls, rotating in opposite direction, and are crushed and ground.
Four-roll crusher
The material are crushed through primary & secondary crushing by upper & lower pair of rolls, and discharged from the bottom of crusher.
The gap between the rolls can be adjusted to obtain required product size.
-
Drive Mode
The traditional double roll crusher is driven by two motors through reducers without mechanical buffer. Power consumption is higher. Double roll crusher designed by ANDE adopts single e-motor, small & big pulley and dual output shaft reducer to drive fixed roll and loose roll, keeping two rolls rotating at constant differential speed. Ball coupling is used to connect fixed roll and reducer to have better impact resistance. Operation is reliable with higher crushing efficiency and lower power consumption.
Four roll crusher is driven by two units of E-motor, reducer, coupling and pulleys. Each pair of roll is driven by one drive unit.
-
Roller
If material is to be crushed smaller with uniform product size, crushing roller shall be cast with multi-element low alloy steel. Surface hardness is between HB260-380 after heat treatment and precise finishing.
If size of material is bigger and moisture content is higher, buildup welding with wear-resisting alloy wire can be adopted for surface of rollers, which can help increase friction coefficient of the rollers and bite into the material.
-
Mechanical/Hydraulic Loading Device
Double-roll/Four-roll crushing rollers are equipped with mechanical or hydraulic loading device, which can protect working rolls when foreign matters enter the machine. It can also be used to adjust the gap between working rolls to compensate the wear consumption of the roll skin. Hydraulic loading is equipped two-cylinder & four-chamber hydraulic cylinder (patent no.: ZL201420846028.2), which has good performance of sync buffering and keeps pressure for long time.
-
Cutting/Grinding Device
When roller is worn or groove & pit at surface occurs, repairing can be done with cutting/grinding device. If surface hardness is too high to cut, specially designed grinding device can be adopted (Patent no.: ZL 2006 2008 1378X). While rotating normally, roller can be ground by quartz wheel, which can reduce repairing job intensity.
Double roll crusher
Model No. |
Output(t/h)
|
Feed size(mm)
|
Product size(mm)
|
Motor power(kw)
|
φ750×500 |
10-25 |
≤30/80 |
5-25 |
30 |
φ750×700 |
15-35 |
≤30/80 |
5-25 |
37 |
φ750×1000 |
20-75 |
≤30/80 |
5-25 |
45 |
Φ1200×1000Y |
35-100 |
≤40/100 |
5-25 |
75 |
Φ1200×1200Y |
45-120 |
≤40/100 |
5-25 |
90 |
Four roll crusher
Model No.
Output(t/h)
Feed size(mm)
Product size(mm)
Motor power(kw)
φ750×500
5-15
≤20/25
3-8
22+18.5
φ750×700
7-20
≤20/25
3-8
22+22
Φ900×700
16-30
≤15/35
3-10
30+30
Φ900×900
20-40
≤15/35
3-10
37+37
Φ1000×1000Y
25-50
≤20/50
3-10
45+45
Φ1200×1000Y
35-60
≤25/75
3-10
55+75
Φ1200×1200Y
40-90
≤25/75
3-10
75+90