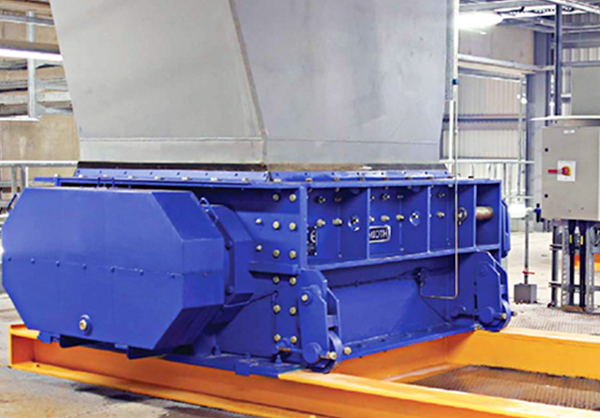
Double roll sizer adopts innovative working principle: subjected to multiple points and time-sharing loading, the material is broken efficiently by exploiting any natural weakness to achieve a three dimensional controlled product size.
Main features:
High throughput capacities up to 5000t/h at low operating cost
Compact and flat design resulting in a low overall height of the crushing plant
Low metallic wear and minimum fines content due to slow rotation speed of rotors
Relatively low power consumption owing to shearing action instead of squeezing and collision
Better adaptability for wet and sticky, smeary and ductile feed materials
Fields of Application
Double roll sizer is used for primary, secondary and tertiary crushing of from wet and sticky materials (bauxite, nickel minerals, clay and etc.) to medium-hard materials (limestone, chalk, lignite, coke, phosphates and etc.).
The material is fed into the machine by means of apron feeder or belt conveyor while the high torque and low speed rotors are running inward or outward. Initially, the material is gripped by the leading faces of opposed rotor teeth and subjected to multi-point loading, which induces stress into the material to exploit any natural weakness. Then the material is broken in tension by tooth faces of rotors. Any lumps remaining oversize are broken as rotors chop through the fixed breaker bars, achieving a three dimensional controlled product size. The teeth of rotors are staggered in deep scroll pattern, which helps to spread the feed across the full length of the rotors. The material can be broken either by counter-rotating rotors of the Center-Sizer (Type 2RCS) running inward or between side crushing comb and the outward rotating rotors of the Side-Sizer (Type 2RSS).
Output depends on rotor length, center distance and rotation speed. Tooth configuration can be suited to individual material and feed size. Product size is mainly decided by center distance, tooth columns & configuration.
-
Drive mode
The two rotors are driven by single or double motors with fluid couplings, hard-faced reducers and couplings. The drive unit can guarantee the machine will start even if large amounts of material are lying on the top of breaker rotors.
Central distance of two rotors is fixed or adjustable. Breaker bars are equipped under the middle of the two rotors to break the feed again.
-
Rotor
The rotor consists of shaft, star-wheels, teeth, bearing boxes and etc.. Star-wheels are fitted on the shaft at a fixed angle difference to keep tooth in a deep scroll pattern, which helps the shaft with balanced force and reduce loading fluctuating. The shaft and star-wheel are specially designed so that replacement of star-wheels is time consuming. The tooth is made of high chrome alloy cast or hard-faced to achieve longer use life. Bearings are lubricated with an autonomous central grease lubrication unit. The unit is monitored in control room with sensors that will trigger an alarm if a malfunction occurs or the grease barrel is empty.
-
Tooth roll
Replaceable cleaning teeth are fitted on the inside of breaker frame to prevent any clogging of rotors. Side frame can be opened up for maintenance.
-
Moving wheels
The double roll sizer can be installed on concrete, or equipped with a whole steel platform, below which a travelling gear unit is assemble to facilitate maintenance.
Model No. |
Output(t/h)
|
Feed size(mm)
|
Product size(mm)
|
Motor power(kw)
|
500 |
100-300 |
≤250 |
25-50 |
160*1 |
625 |
200-600 |
≤300 |
60-100 |
160*2 |
750 |
300-800 |
≤350 |
75-125 |
315*1 |
1000 |
600-2500 |
≤1000 |
200-300 |
220*2 |
1250 |
1000-6000 |
≤1300 |
200-350 |
355*2 |
1500 |
4000-14000 |
≤1300 |
250-400 |
550*2 |